영상 참조 : https://youtu.be/5hqR4hGHyU4
전 세계가 태양과 같이 수소를 핵융합시켜 무한에 가까운 에너지를 만드는 ‘핵융합발전’ 기술 연구에 뛰어들고 있다. 한국의 핵융합로가 태양 중심부 온도인 1500만 도보다 6배 높은 1억도 유지 기록을 최대 8초로 갈아치우며 기술을 이끄는 가운데 한국의 기업들 또한 높은 기술력으로 세계 곳곳의 핵융합 실험장치를 만드는 주역으로 활약하고 있다.
한국 독자 기술로 개발된 KSTAR는 제작에 한국의 기업들이 다수 활약했다. 이 기술력을 바탕으로 한국의 기업들은 프랑스 카다라슈에 건설되고 있는 국제 핵융합 프로젝트 ‘국제핵융합실험로(ITER)’에서도 핵심 설비 제작을 담당하고 있다. ITER는 핵융합에너지 실증을 위해 한국과 미국, 유럽, 러시아, 일본, 중국, 인도 등 7개국이 공동으로 개발해 건설과 운영을 담당하는 실험로다. 79억 유로(약 10조 4500억 원)가 투입돼 2025년 완공을 목표로 개발되고 있다. KSTAR 개발에도 참여한 기업인 SFA는 ITER의 열차폐체 개발과 제작 전 과정을 책임지고 있다. 열차폐체는 ITER 핵심 부품으로 핵융합로 속 1억 도 플라즈마와 외부에서 플라즈마를 유지시켜 주는 영하 269도 초전도 자석 사이의 열전달을 최소화해 실험로를 안정적으로 유지해주는 설비다. 높이 12m, 지름 25m에 무게 900t에 이르는 초대형 구조물이다. SFA는 열차폐체 설계와 여러 기업에 분배된 다양한 열차폐체 부품 제작을 총괄하고 있다. 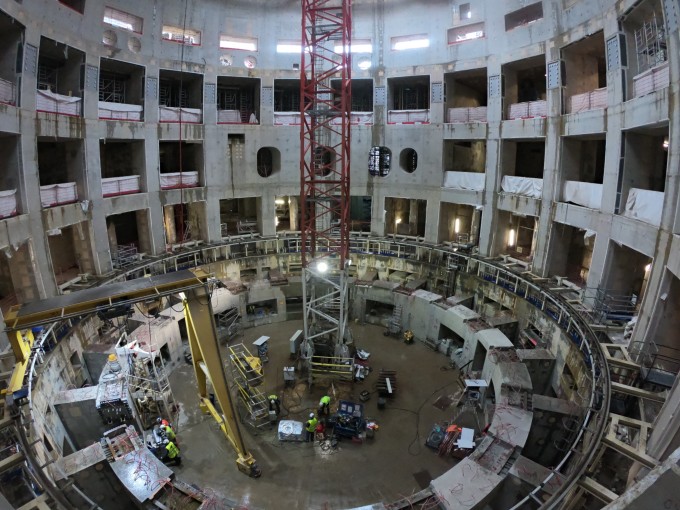 프랑스 카다라슈 국제핵융합실험로(ITER) 건설 현장. 초전도 핵융합로(토카막)가 들어설 본관 내부의 모습이다. 동아사이언스DB SFA는 열차폐체 기능의 핵심인 복사열 차단을 위한 은도금 작업 또한 진행하고 있다. 은은 전파를 쉽게 반사하는 성질을 가져 전파를 통해서 전달되는 복사열이 열차폐체 내부에만 머물고 바깥으로 빠져나오지 못하게 한다. SFA는 대형 구조물을 한 번에 도금하기 위해 가로 9m, 세로 3m, 깊이 6m 수조 11개가 일렬로 서있는 대형 도금 설비를 새롭게 제작했다. 각종 화학 약품으로 가득찬 수조 11개에 열차폐체 부품을 일일이 넣었다 빼는 과정을 거쳐야만 은색 광택이 나는 부품들이 제 기능을 갖는다. 경남 창원의 발전설비 업체인 삼홍기계는 열차폐체의 몸통을 만들고 있다. 열차폐체는 크기가 어마어마한 만큼 전체를 한 번에 만들 수 없다. 대신 전체를 9개로 정확히 나눠 만든 후 프랑스 ITER 건설현장에서 하나로 합치게 된다. 합쳤을 때 마치 처음부터 한 몸이었던 것처럼 만들기 위해 높이 12m에 달하는 장비지만 오차는 2mm에 불과하도록 제작하는 정밀 공정이 필요하다. 삼홍기계는 600개의 패널과 7만 개의 볼트로 구성되는 열차폐체 하나하나가 모두 같은 모양을 띄도록 만들고 있다. 삼홍기계는 7년의 제작기간 중 3년을 연구개발에만 투자했다. 거대한 본품 하나를 만들고 버리는 과정을 거쳤고, 거대한 설비를 제작하기 위해 아예 공장 한 동을 새로 차렸다. 조래진 삼홍기계 대표는 “철재 구조물을 만들 땐 오차율이 2%만 돼도 잘 만든다는 소리를 듣지만 열차폐체는 0.02%까지 떨어져야 한다”고 말했다. 삼홍기계는 9개 조각 중 8개 제작을 완료했다. 지난해 9월에는 첫 초도품이 프랑스 카다라슈로 운송됐다. 현재는 마지막 조각의 제작에 박차를 가하고 있다. 경남 함안 TMC는 열차폐체에 액체 헬륨을 공급할 파이프를 제작하고 있다. 액체 헬륨은 열차폐체를 식히는 냉각수 역할을 한다. 1억 도에 달하는 열을 가두기 위해 ITER 곳곳에 피처럼 공급된다. 사람의 동맥이 끊어지면 죽는 것처럼 ITER의 파이프 또한 누수가 없어야 한다. 파이프의 누수는 파이프와 파이프 사이 용접에서 주로 발생하기 때문에 누수를 줄이려면 용접 횟수를 최소화해야 한다. TMC는 용접 횟수를 줄일 수 있는 ‘T자 뽑기’ 기술을 ITER 파이프에 적용하는 공정을 개발했다. T자 뽑기는 파이프에 구멍을 뚫은 후 추를 집어넣고 끌어올려 구멍 부위를 화산처럼 볼록 튀어나오게 하는 기술이다. 기존엔 용접을 두 차례 이상 해야 했지만 T자 뽑기가 적용된 구멍은 둘레를 따라 한 번만 용접을 하면 된다. 기존 두께 1mm 파이프에는 쓰이던 기술이지만 ITER에 활용되는 두께 3.05mm에는 처음 시도됐다. TMC는 트럭 2대 분량에 달하는 파이프를 버려가며 반복 시도한 끝에 최적의 공정을 개발해냈다. ITER로 이미 배송한 1차 물량은 전량 합격점을 받았고 2차 물량도 제작을 올해 중순 완료할 계획이다. 한국에서 ITER 제작에 참여하고 있는 업체는 224개사다. 미래가 불투명한 핵융합 기술 개발에 나선데 대해 이들은 기술에 대한 확신 때문이라고 입을 모은다. 60대인 조 대표는 “핵융합 기술의 혜택을 살아있을 때 볼 수 있을까 생각한다”면서도 “좋은 기술이 적용되는 만큼 빠른 상용화가 가능할 거라고 믿는다”고 말했다. 기업들은 정부가 핵융합발전 투자를 지속해 생태계를 유지해 줘야만 기술 또한 유지될 것이라고 조언한다. 조 대표는 “기술이 축적되다 보니 시행착오를 겪지 않고도 경쟁력있게 좋은 품질의 물건을 만들 수 있다”며 “공사 진행을 위해 투자한 많은 설비를 바로 활용할 수 있는 추가 투자가 필요하다”고 말했다. 이형민 TMC 대표는 “한국의 핵융합 기술에 대해서는 확신을 가진다”며 “중국이 후발 주자로 따라오는 만큼 국가 차원에서 투자가 이뤄져야 성과를 누릴 수 있을 것”이라고 말했다. |